The evolving designer ecosystem
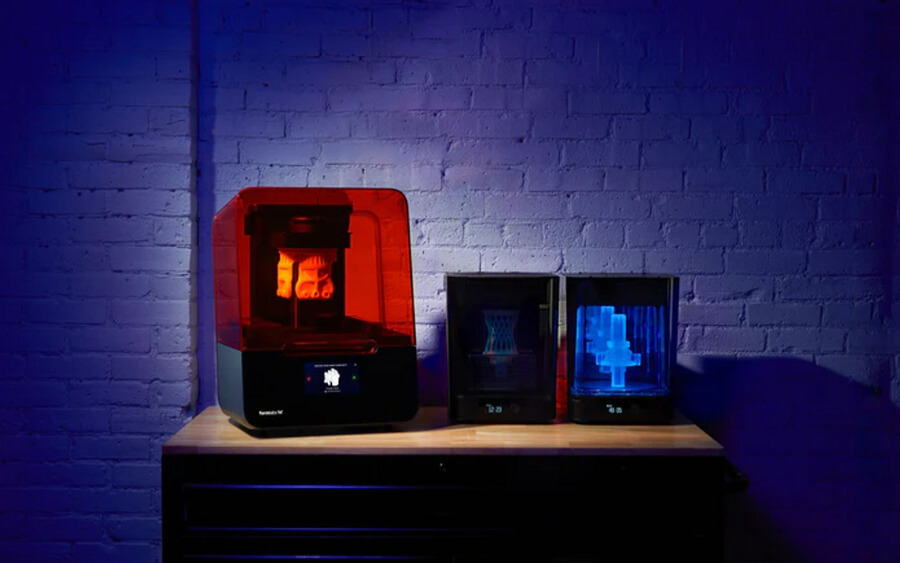
There are now various tools to accelerate the initial conceptual phases of the design process. The graphic tablet has replaced the old drawing board, shapes can be fashioned by 3d printers, and AR/VR is now officially within reach.
“Years ago, we would start from a sketch that we would give to a sculptor,” explained Nicolas Lebrun, Head Designer at our (big) sister company, Creaform. “The sculptor would make a model based on the sketch and then provide us with a sculpture. We would then try to reproduce their work into our CAD software. Just getting the sculpture could easily take a month. And the project was not over; it was just beginning!”
Nowadays, there are tons of new tools to make the design process more efficient without cutting down on the romantic part of it all.
The most significant ones are 3D scanning and 3D printing, as they offer a quick way in and out of computerized design steps.
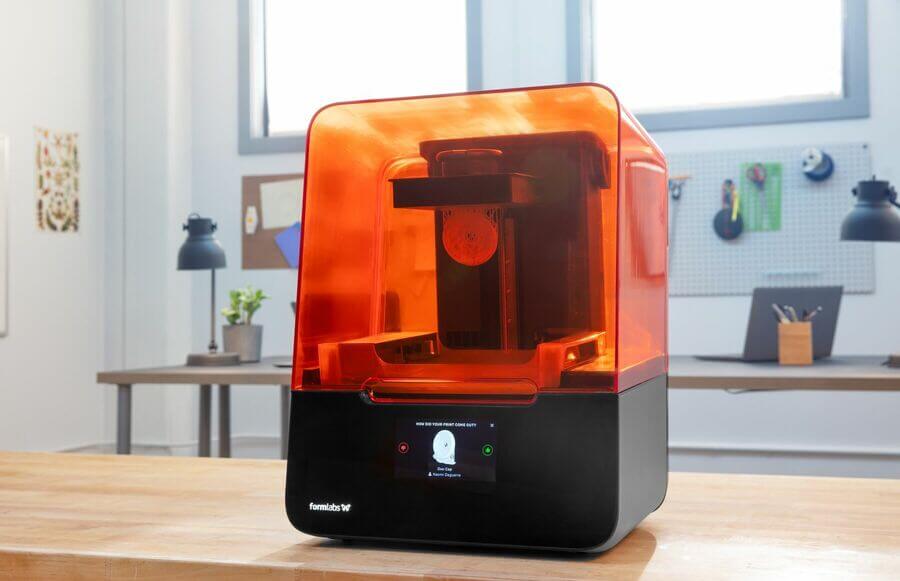
Fig 1: A typical designer’s workshop with Formlabs as its centrepiece.
Improved workflows
Projects typically start with a sketch and, with modelling software getting more user-friendly and accessible, the product designer may create a rough model by themself. Some designers prefer to work with their hands and fashion their first iterations out of typical modelling materials (foam, cardboard, clay); others, like Nic, will instead start their design with CAD directly. Once the rough model is completed, it can be produced using a 3D printer.
“I sometimes keep entire areas empty on my preliminary models. Instead of guessing what the perfect fit will be, I leave the area empty and fill it with sculpted clay afterwards,” Nicolas explained. “It is spectacular what a small variation can have on the look and feel of a given object. Sculpting it directly gives you that feel instantly.”
This iterative process allows the designer, using a 3D scanner and 3D printer, to jump in and out of a computerized process. “Making the exact shape you have in mind is easier and more direct by hand but then, making it perfectly symmetrical is much easier and faster on a computer; this is where both methods work so well together.”
Interested in 3D scanning?
Contact our peel 3d experts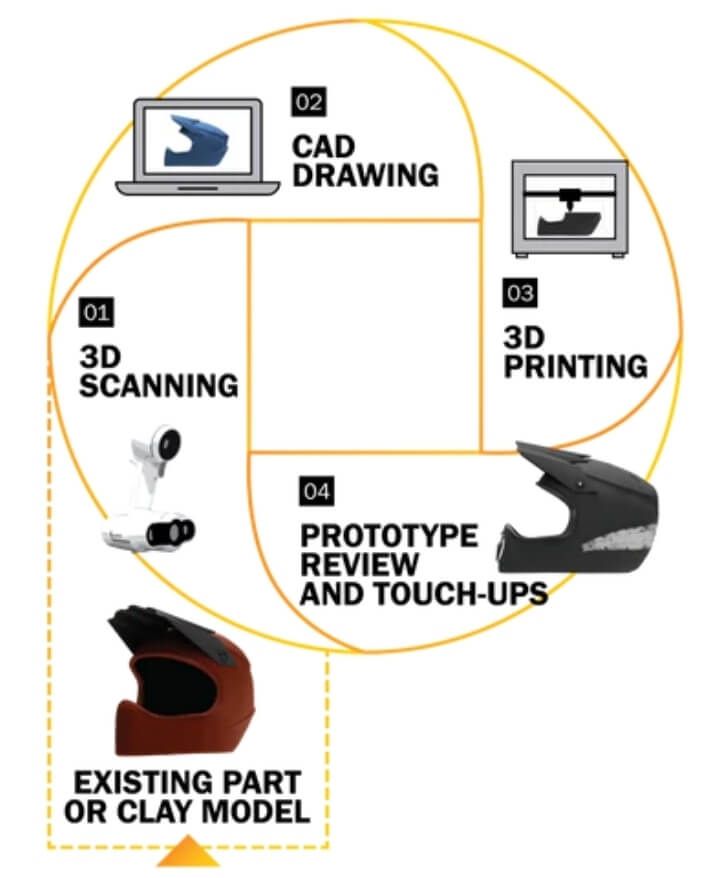
Fig 2: Collaboration of 3D scanning and 3D printing in a modern design process
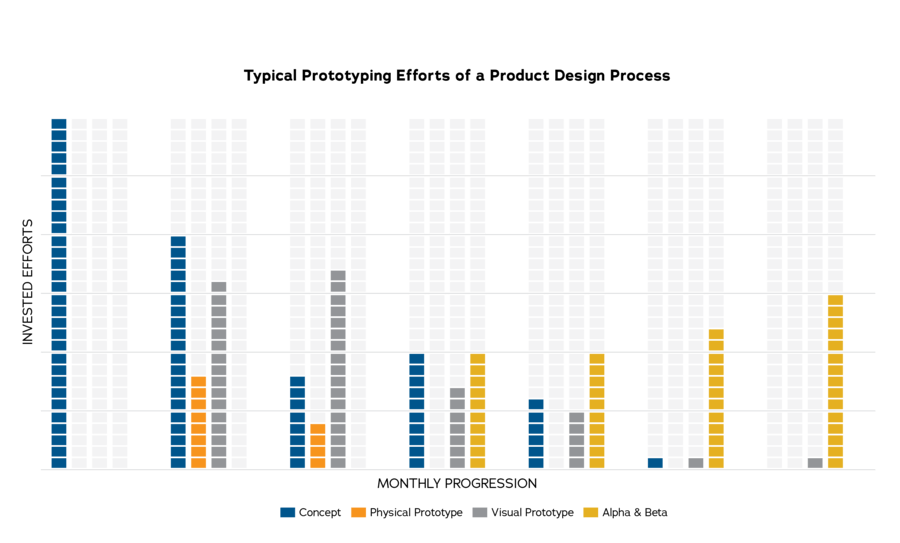
Many iterations and prototypes are produced throughout this process, which is why saving even a little time on each prototype design cycle is so valuable in the end.
Opportunities to be bolder
“Of course, more efficient tools shorten the time it takes to run a design cycle. They allow you to bring new designs to the market faster. However, there are other benefits as well,” Nicolas pointed out. “Working faster during a given period can also let you consider more options and try new things. Ultimately, having more time available to test different options brings your project closer to perfection!” Designs can therefore be bolder or simply better adapted to their applications.
The shared roots
Even more interesting is that the process described above is pretty much the same regardless of the product you are making. A product designer working on the latest pair of running shoes will use a design process comparable to one working on the newest bike helmet, for instance or even on furniture design.
All designers have their way of working and preferred tools; a 3d scanner with a smaller field of view and a higher resolution will be better for scanning a running shoe as an example, while one with a larger field of view will work better on more oversized furniture. Clay may work better for a specific type of project while silicone moulding and plaster will be more suitable for others… but ultimately, it all comes down to the same thing.
Worn Running Shoe scanned with Peel 2 - 3D model by Peel-3D.com
In the design engineering jungle, competition is fierce. Only the manufacturers that can produce high-quality products the fastest will survive. Software intelligence, augmented reality, and future technology developments will undoubtedly bring further progress in how products are designed. The day when products design themselves has yet to come. Until then, the fittest product designers will be there to create the innovative objects we use in our daily lives.
When working on a design, the typical process usually involves concepts, designs sketched on a sheet of paper. Ideas then lead to physical prototypes (functional concepts that do not fully consider the visual design). Then follow the visual prototypes (concepts that are more faithful to the design but do not integrate the internal components). Both physical and visual are combined to create alpha and beta prototypes (preproduction models that work and look like the final product). These steps usually overlap considerably, as shown below:
Wonder how Peel 3D can transform your work, solve problems, and save you time?
Contact our Peel 3D expertsauthor
ABOVE MENTIONED PRODUCTS
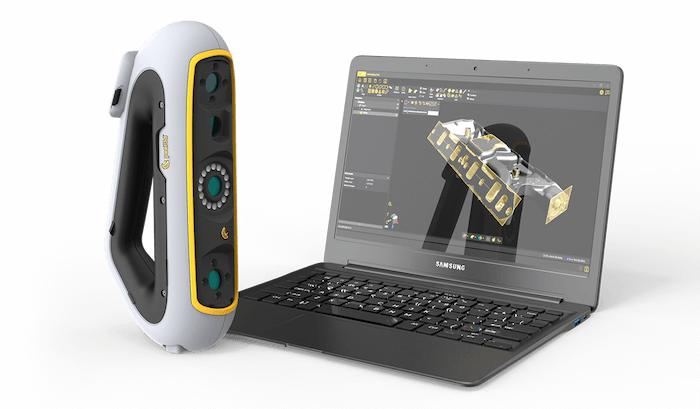
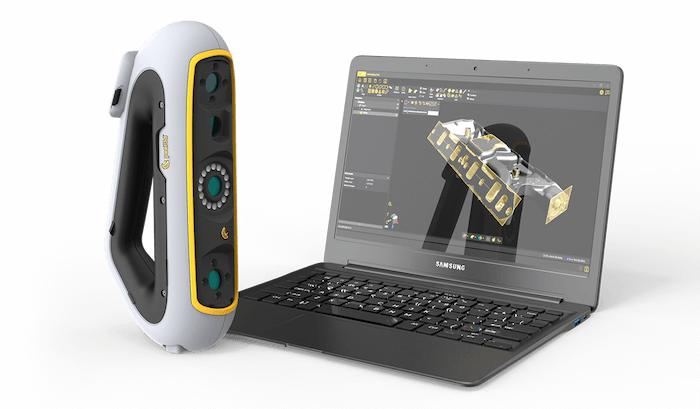