Intro to 3D Scanning Technology and Its Applications
In recent years, 3D scanning has emerged as a powerful technology that has transformed various industries, from manufacturing and architecture to healthcare and entertainment. By capturing the geometry and physical characteristics of real-world objects, 3D scanning enables the creation of digital representations that can be used for analysis, design, visualization, and more. In this article, we will explore the fundamentals of 3D scanning, the different technologies available, their strengths and limitations, and the diverse applications of this revolutionary technology.
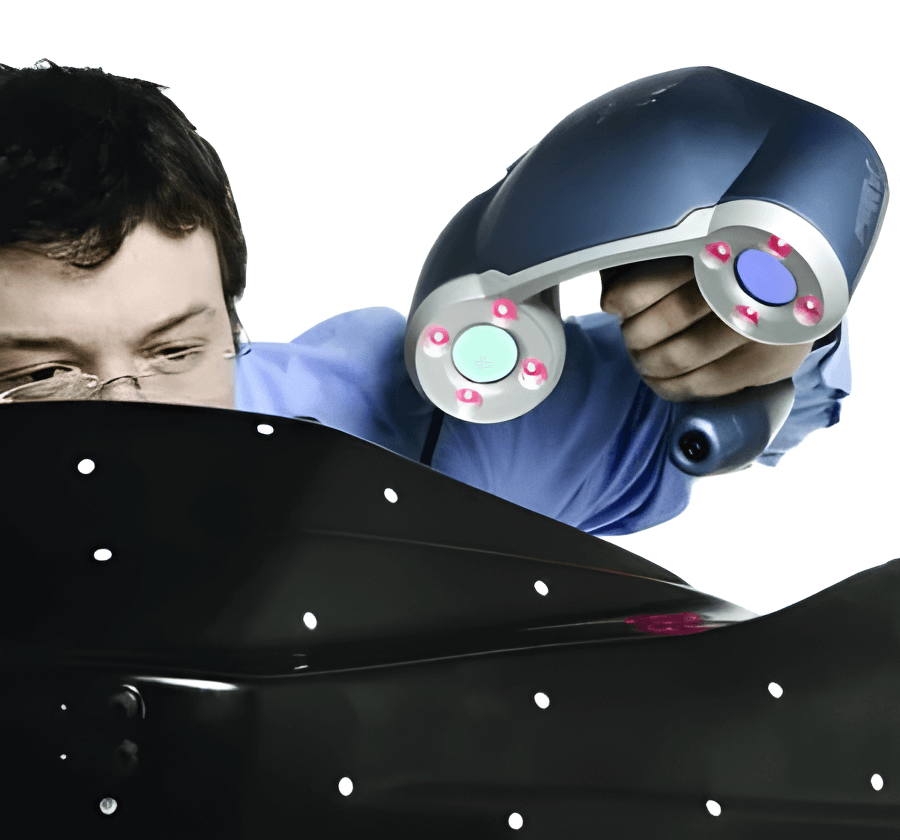
The original REVscan in action, one of the first handheld portable 3d scanner available on the market.
Understanding 3D Scanning:
At its core, 3D scanning involves capturing the shape, texture, and sometimes color of a physical object and converting it into a digital 3D model. This process requires specialized hardware and software to accurately measure the object's geometry and surface properties. Let's delve into the different technologies commonly used in 3D scanning and explore the principles behind them:
Laser Scanning:
Laser scanners employ the principle of triangulation to measure distances and create a point cloud representation of an object's surface. They emit laser beams that bounce off the object, and the reflected light is detected by sensors. By analyzing the time it takes for the light to return, precise distance measurements are obtained. These measurements are combined with the scanner's position and orientation to construct a 3D model of the object. Laser scanners excel in capturing complex geometries, offering high accuracy and detailed results. They emit a laser line or a single laser point onto the object's surface and record the position and orientation of the reflected light, generating a dense point cloud. The point cloud is then processed to create a mesh or a solid model representing the object's shape.
Interested in 3D scanning?
Contact our peel 3d expertsStructured Light Scanning:
Structured light scanners utilize the projection of a known pattern of light onto the object's surface. These patterns can be grids, stripes, or even complex shapes. By projecting the pattern and capturing its deformation using cameras, the 3D shape of the object can be reconstructed. The deformation occurs due to the variation in the object's surface relative to the projected pattern. Structured light scanners work by analyzing the distortion of the projected pattern in the captured images. The distortions provide information about the depth and shape of the object's surface. The captured images are processed using algorithms to extract the 3D coordinates of the object's points, resulting in a detailed 3D model.
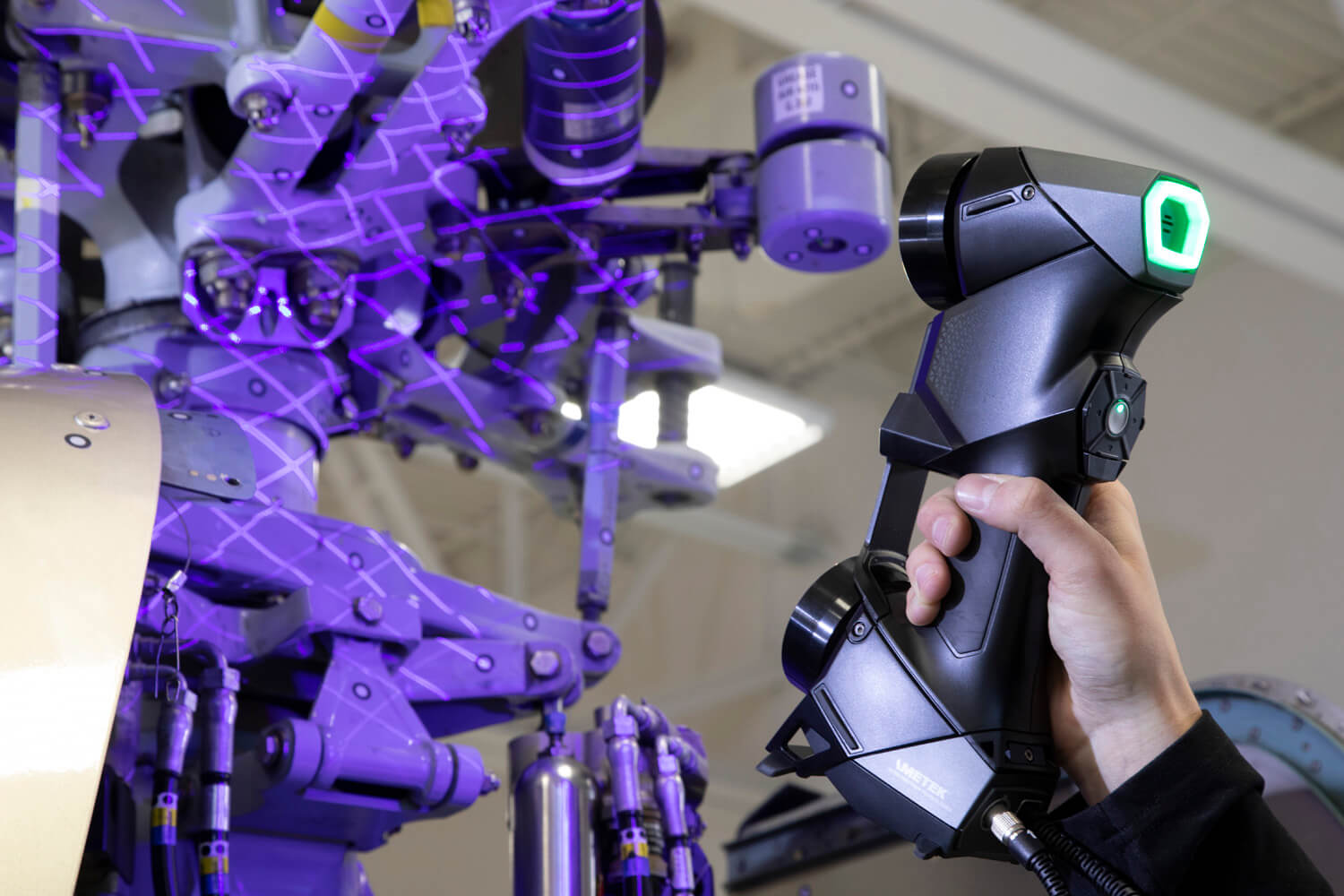
Several generations later, the HandySCAN BLACK stands as a testament to years of relentless research and development, solidifying its position as one of the most cutting-edge structured light scanners in the world.
Photogrammetry:
Photogrammetry involves capturing multiple images of an object from different angles and using specialized software to analyze common features and calculate their spatial relationships. The images are usually captured using digital cameras. The software identifies matching features in the images, such as distinct points or patterns, and determines their 3D positions based on the differences in their appearances in the images. By triangulating these points, a 3D model can be reconstructed. The accuracy and quality of the 3D model depend on the number and distribution of the images, the quality of the camera, and the accuracy of the feature matching algorithms used in the photogrammetry software.
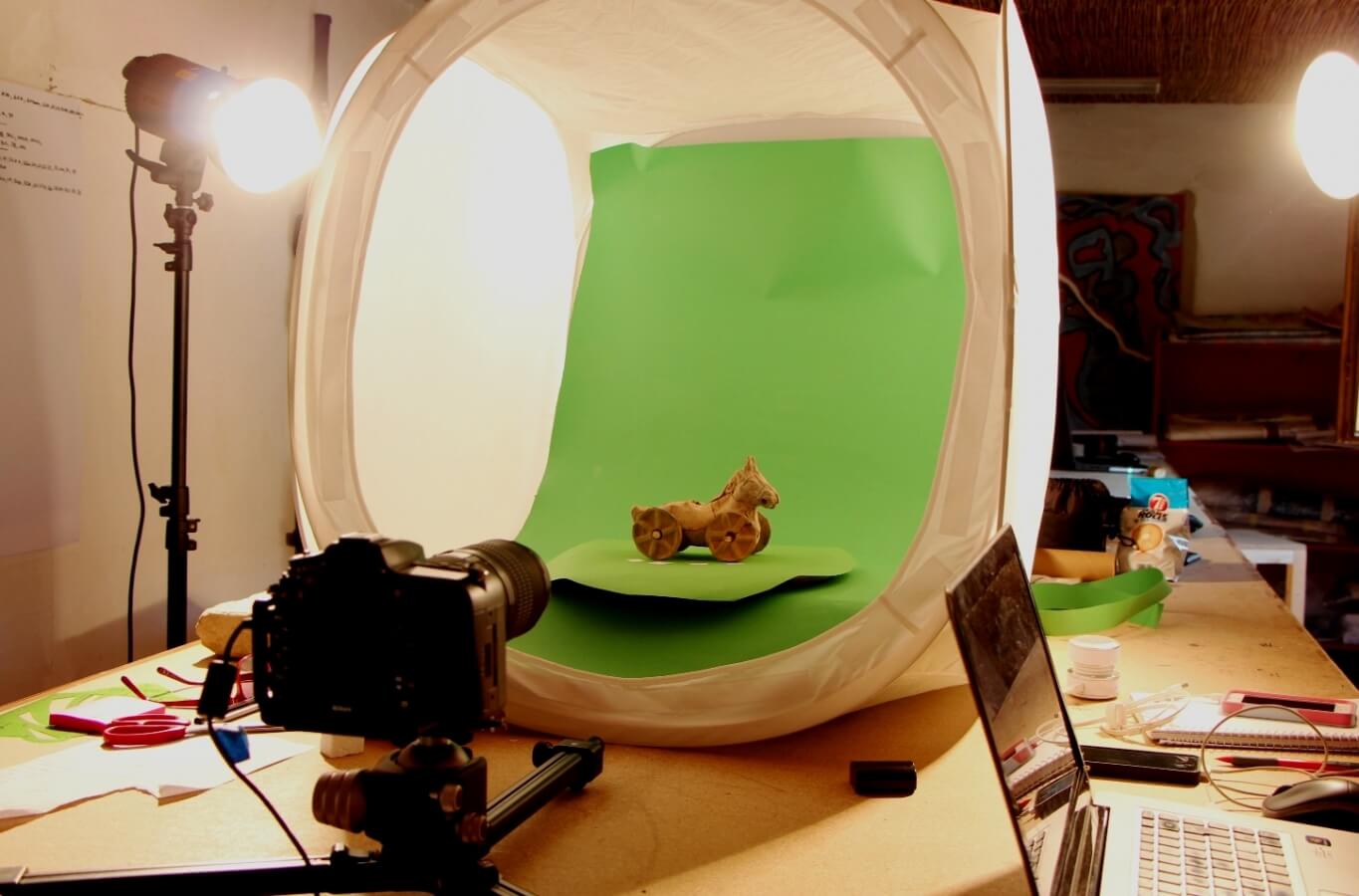
A photogrammetry system with proper lighting to capture the shape of a simple artifact.
Time-of-Flight (ToF) Scanning:
ToF scanners utilize infrared sensors to measure the time it takes for light to travel to an object and return. These scanners emit short bursts of infrared light and measure the time it takes for the light to bounce back. By calculating the speed of light, ToF scanners determine the distance to each point on the object's surface. This information is used to construct a 3D model. ToF scanners offer real-time scanning capabilities, making them suitable for applications like augmented reality and gaming. They capture the entire scene simultaneously and can quickly generate a 3D model of the environment.
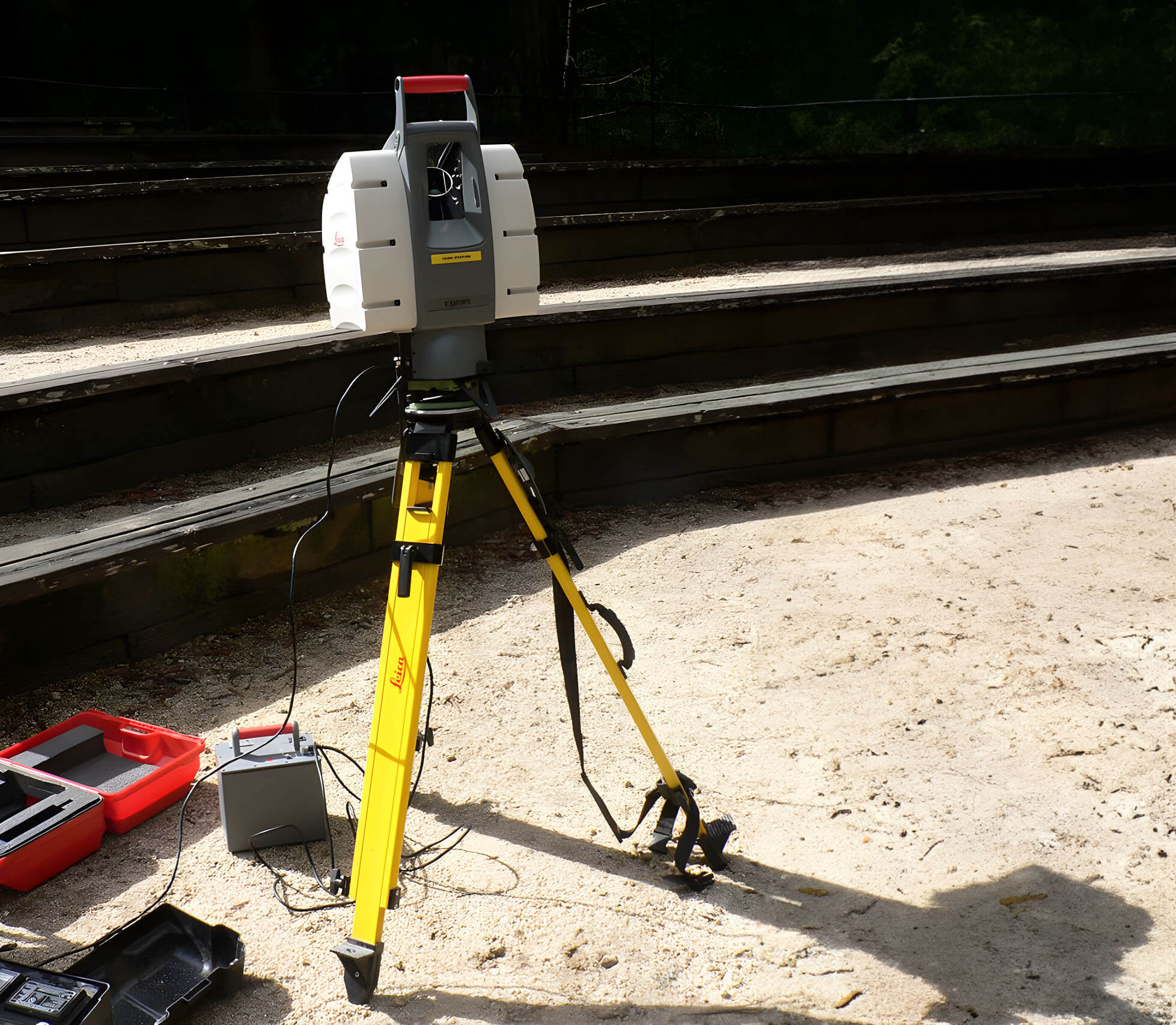
A typical LIDAR system usable scan buildings, rock formations, etc. and produce 3D data.
Each 3D scanning technology operates on unique principles but shares the common goal of capturing the physical characteristics of objects in the form of digital 3D models. These models can then be further processed, analyzed, and utilized in various industries and applications. It's important to consider the strengths and limitations of each technology to choose the most suitable approach based on the specific requirements of a project.
Strengths and Limitations:
- Laser scanning offers high accuracy and detailed results, making it suitable for precise measurements and complex geometries. However, it can be expensive and requires controlled lighting conditions.
- Structured light scanning is more affordable and portable, making it a versatile option for various applications. Nonetheless, it may struggle with reflective surfaces and sometimes requires consistent lighting.
- Photogrammetry is accessible, cost-effective, and flexible in capturing large objects or environments. However, it can be sensitive to environmental factors and texture variations.
- ToF scanning provides real-time capabilities and is well-suited for applications like augmented reality and gaming. However, it may not capture fine details as accurately and can be influenced by ambient lighting.
Applications of 3D Scanning:
The applications of 3D scanning are extensive and span across various industries.
- Manufacturing and Engineering: 3D scanning facilitates quality control, reverse engineering, and prototyping. It enables precise measurements, dimensional analysis, and the creation of digital models for design and simulation.
- Architecture and Construction: 3D scanning aids in capturing as-built conditions, creating accurate models for renovation or restoration projects, and facilitating clash detection during the design process.
- Healthcare: 3D scanning plays a vital role in creating patient-specific implants, prosthetics, and orthotics. It enables the digitization of anatomical structures for surgical planning, visualization, and medical education.
- Entertainment and Gaming: 3D scanning allows for the creation of realistic and detailed 3D characters, objects, and environments in movies, video games, virtual reality (VR), and augmented reality (AR) applications.
- Cultural Heritage Preservation: 3D scanning preserves and digitally archives historical artifacts, sculptures, and archaeological sites, facilitating conservation efforts, research, and virtual museum experiences.
3D scanning technology has revolutionized numerous industries, enabling the capture of real-world objects in incredible detail and accuracy. By leveraging various scanning techniques such as laser scanning, structured light scanning, photogrammetry, and time-of-flight scanning, organizations can achieve precise measurements, create digital models, enhance design processes, and improve efficiency. While each technology has its own strengths and limitations, the collective impact of 3D scanning is undeniable, offering new possibilities in manufacturing, healthcare, architecture, entertainment, and cultural heritage. As advancements continue to push the boundaries of 3D scanning, we can expect even more innovative applications and transformative solutions in the future.
Wonder how Peel 3D can transform your work, solve problems, and save you time?
Contact our Peel 3D expertsauthor
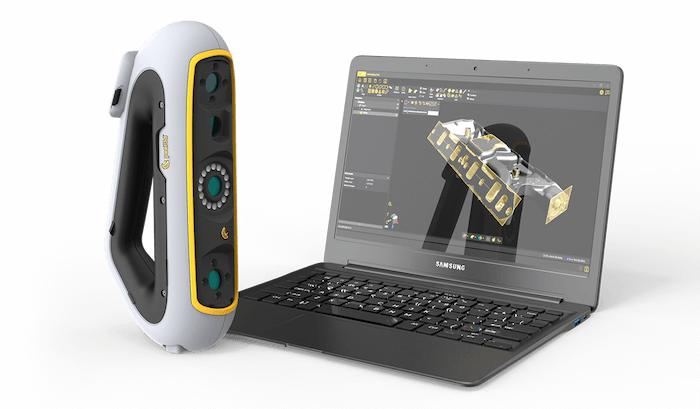